Chemical Recycling
- Karen Flanagan
- Jul 26, 2023
- 3 min read
Updated: Dec 24, 2023
Plastic waste is mostly recycled mechanically – shredded, melted and shaped into new products.
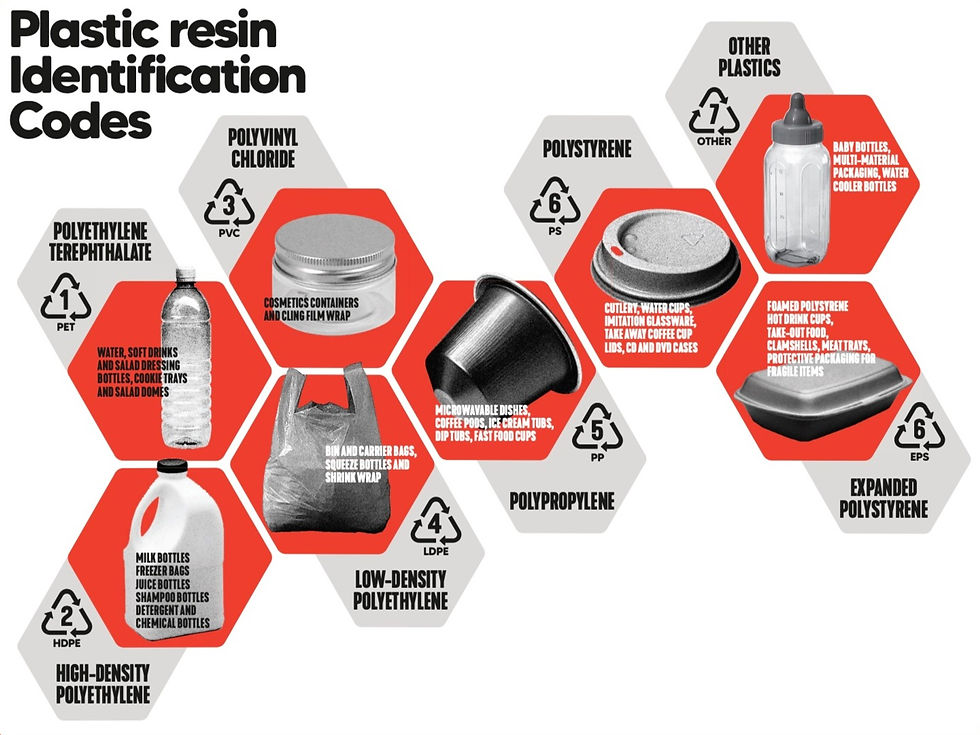
The UN has stated: 'chemical recycling offers a promising solution in complement to mechanical recycling'. Yet Greenpeace has called this a false solution. Let’s look at the evidence.
What is ‘Chemical Recycling’?

Plastics are polymers – long chains made from smaller molecules called monomers. Chemical recycling aims to break down plastic polymers into monomers and use the monomers to make new plastics. This could potentially create a circular economy for plastics.
However, it’s not as easy as it looks. Plastics are incredibly stable and huge amounts of energy are used to break plastics down into monomers. For example, Mura Technology’s hydrothermal recycling process requires high temperatures and pressures.
Techniques exist to convert waste plastics into alternative plastics for new products – but these are also energy intensive. The phrase ‘chemical recycling’ is also used when waste plastics are converted into fuels – but this is not recycling, says the UN.
There are concerns about current chemical recycling processes. However, the UN recognises this technology is still evolving. So what does the future hold?
Catalysts – Current Research
Catalysts can lower the energy required for a chemical reaction. Much work has gone into engineering enzymes (biological catalysts) to break down plastics. This is easier for plastics which contain carbon-oxygen bonds, such as PET. Enzymes tailored to different plastics cut the polymer chains into monomers. However, due to plastic pretreatment steps, it is estimated enzymatic recycling will use more energy and emit more greenhouse gases than mechanical recycling. For example, enzymatic chemical recycling of PET requires high temperatures to soften the plastic.

Polythene, polypropylene, PVC and polystyrene – which account for 65% of plastic waste – need to be oxidised (have oxygen added to the polymers) before they can be broken down by enzymes, complicating the process. A study has shown enzymes in the saliva of the waxworm oxidise and break down polythene at room temperature. But the molecules produced are not monomers or plastic – so not a circular economy – and it is not clear how they could be used.
Chemical catalysts have been used to decompose polythene and polypropylene waste, but most of the products are fuels – again, not a circular economy, and not recycling. However the conversion of polythene into propylene – the monomer for polypropylene – has been achieved using moderate temperatures. Polythene has also been upcycled into aromatic molecules which could be used in paints, lubricants, and other consumer products.
A method using enzymes and sunlight has been used to convert CO2 and PET into syngas (used industrially to produce ammonia, methanol and hydrogen) and glycolic acid (used in the cosmetics industry). This is not a circular economy, but it is low energy and could process two waste streams (CO2 andPET) and produce syngas, which is currently obtained from fossil fuels. However, the technology is still in development.
To summarise…
In the future, chemical and biological catalysts may provide lower energy chemical recycling options, but this technology is in its infancy and would still require waste plastics to be collected and sorted. This has proven extremely difficult historically, with only 9% of plastic waste recycled. This issue could be addressed by the development of truly biodegradable polymers, not based on fossil fuels, which break down in the appropriate environments.
Current chemical recycling processes are energy intensive, and emit toxins. Plastic recycling has been linked to toxic plastics and microplastic pollution. This is why Greenpeace is calling for a focus on reducing plastic production and use.
How to Get Involved?
Ask the UK government to Fix the plastic waste crisis.
+++++++++++++++++
For more information contact: info@scarabtrust.org.uk
Images:
'Plastic Resin Identification Codes' by Greenpeace
Monomer/ Polymer infographic by Author
'Waxworm' by wykesgerald on Flickr